Process Safety Management
The Power of Proactive and Preventive Approaches in Disaster and Accident Prevention
In the realm of industrial safety and disaster management, the adage “an ounce of prevention is worth a pound of cure” couldn’t be more apt. Embracing a proactive and preventive approach is not just good; it’s paramount for averting disasters and accidents within the industry.
Why we focus on prevention?
- Risk Identification and Mitigation: Proactive measures involve identifying potential risks before they escalate. By conducting thorough risk assessments, industries can pinpoint vulnerabilities in their operations and infrastructure. With this knowledge, they can take corrective actions to mitigate these risks, reducing the likelihood of accidents or disasters occurring.
- Environmental Protection: Many industrial accidents have far-reaching environmental consequences. A proactive approach helps prevent spills, emissions, and other incidents that can harm ecosystems and natural resources. Protecting the environment is not just a legal requirement but also an ethical responsibility.
- Regulatory Compliance: Proactive safety measures help industries remain in compliance with regulatory standards. Compliance not only reduces the risk of legal actions and penalties but also ensures that operations are aligned with industry best practices.
- Safety Culture enhancement: A proactive and preventive approach fosters a culture of safety within an organization. When employees see that their employer values safety and is committed to preventing accidents, they are more likely to follow safety protocols and be vigilant. This, in turn, reduces human error—a significant contributor to accidents.
- Cost Savings: Preventing accidents and disasters is not only morally sound but also financially prudent. The costs associated with responding to and recovering from accidents far outweigh the expenses of prevention. Insurance premiums, regulatory fines, legal fees, and property damage can be astronomical, making prevention an economically wise choice.
- Reputation and Stakeholder Trust: Industries with a strong track record of disaster and accident prevention build trust among stakeholders. Customers, investors, regulators, and communities are more likely to have confidence in organizations that prioritize safety. This trust can be invaluable in maintaining positive relationships and sustaining business operations.
- Business Continuity: Disasters and accidents can disrupt operations, leading to downtime, lost revenue, and customer dissatisfaction. A preventive approach ensures that essential processes and backup systems are in place to maintain business continuity even in the face of unexpected events.
- Innovation and Efficiency: Proactive industries often invest in innovative technologies and practices to prevent accidents. These innovations can lead to increased efficiency, reduced waste, and improved overall performance.
Proactive PSM: Protecting People, Assets and the Environment
Process Safety Management (PSM) is a systematic approach used in the process industry to prevent and mitigate incidents involving the release of hazardous materials or energy. PSM is particularly crucial in industries where the handling of chemicals and potentially dangerous processes is common. It encompasses a set of principles, practices, and procedures designed to identify, understand, and manage the risks associated with these operations.
It helps bring these benefits to the industry thereby supporting business continuity.
Safety Enhancement
- Incident Prevention
- Compliance with Regulations
Environmental Protection
Improved process reliability
Risk Reduction for Communities
- Enhanced Reputation
Asset Protection
Insurance Cost Reduction
Increased Efficiency and Productivity
PSM promotes a culture of continual improvement. As organizations systematically address process inefficiencies and risks, they often find ways to streamline operations, resulting in increased efficiency and productivity
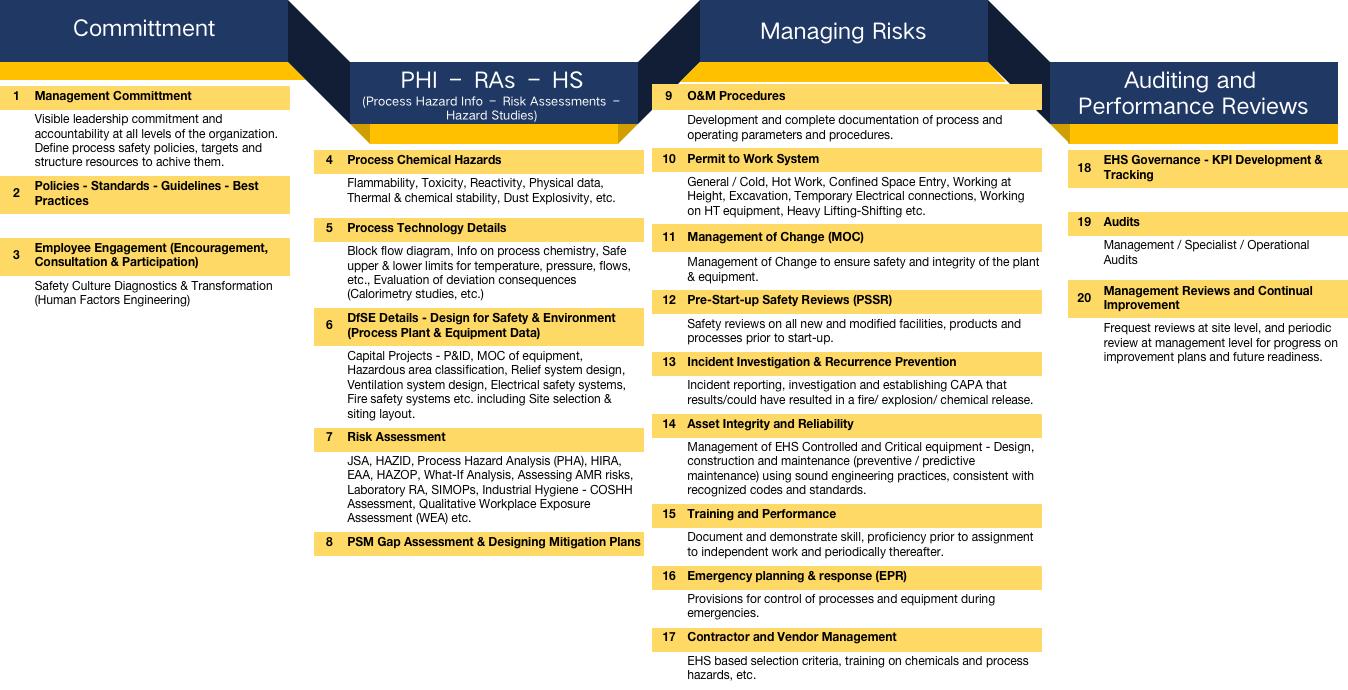
Commitment
Management commitment towards EHS is not only a legal and ethical obligation but also a strategic advantage and hence a critical aspect of ensuring a safe and sustainable work environment within an organization. When top management demonstrates a strong commitment to EHS, it sets the tone for the entire organization and promotes a culture of safety and responsibility. Organizations that prioritize EHS tend to experience reduced accidents, improved employee morale, enhanced reputation, and long-term sustainability. Demonstrating a strong commitment to EHS is an investment in the well-being of employees, the protection of the environment, and the overall success of the organization.
EHS policies and standards are essential for organizations across industry sectors. They provide a framework and guidance for managing risks, protecting employees and the environment, ensuring compliance with laws and regulations, and promoting a culture of safety and responsibility. They are essential tools for organizations to ensure safety, protect the environment, meet legal requirements, and enhance their overall performance. They contribute to long-term sustainability, protect the health and well-being of employees and communities, and positively impact the bottom line.
Employee engagement in EHS matters is crucial for creating a safe and responsible workplace. When employees are actively involved in EHS initiatives, they become partners in maintaining a safe environment, preventing accidents, and promoting a culture of responsibility. Some of the key aspects of employee engagement in EHS matters include Encouragement, Consultation, Participation in EHS Committees, Training and Education, Hazard Identification and Reporting, Near Miss Reporting, Safety Suggestions and Improvement Ideas, Involvement in Emergency Response, Safety Culture Surveys, Recognition and Rewards, Clear Communication, Leading by Example, Continuous Improvement, Empowerment, Metrics and Goals etc.
By actively involving employees in EHS matters, organizations tap into their collective knowledge and commitment to creating a safer and more responsible workplace. Engaged employees are more likely to take ownership of safety practices, contribute to hazard prevention, and help build a positive EHS culture within the organization.
Process Hazard Info – Risk Assessments – Hazard Studies
Process chemical hazards refer to the potential dangers associated with the handling, storage, transportation, and use of chemicals in various industrial processes. These hazards can pose risks to human health, the environment, and the overall safety of the workplace. Identifying and mitigating process chemical hazards is crucial to prevent accidents, injuries, and environmental damage. Some common process chemical hazards include,
Chemical Exposure: Exposure to toxic chemicals, either through inhalation, skin contact, or ingestion, can result in acute or chronic health effects. This includes respiratory problems, skin irritations, chemical burns, and long-term illnesses.
Flammability and Explosivity: Some chemicals are highly flammable or explosive when exposed to heat, sparks, open flames, or incompatible substances. These hazards can lead to fires, explosions, and related injuries.
Reactivity: Chemicals can react violently with other substances or conditions, such as water, air, or incompatible materials. These reactions can release toxic gases, generate heat, or cause explosions.
Corrosion: Corrosive chemicals can damage equipment, infrastructure, and protective gear. They can lead to equipment failure, leaks, and structural damage.
Chemical Storage and Handling: Improper storage and handling practices can result in chemical spills, leaks, or releases. These incidents can contaminate the environment, harm employees, and damage equipment.
Pressure Hazards: Some chemicals are stored or processed under high pressure. A sudden release or rupture of pressure vessels or pipelines can result in catastrophic accidents.
Toxic Gas Releases: Gases, such as chlorine or ammonia, can be released into the atmosphere due to leaks or accidents, posing immediate health risks to nearby workers and residents.
Dust Explosions: Fine powders or dust particles generated during chemical processes can become explosive when suspended in the air. Dust explosions can occur in manufacturing plants, especially those handling combustible materials.
Chemical Incompatibility: Mixing incompatible chemicals can lead to hazardous reactions, including the release of toxic gases, fires, or explosions. Chemical compatibility charts and guidelines help prevent such incidents.
Process technology refers to the techniques, equipment, and methodologies used in chemical and industrial processes to transform raw materials into finished products. It encompasses a wide range of industries, including chemicals, food and beverages, pharmaceuticals, and manufacturing. Here are some key aspects and details of process technology:
1. Process Equipment
2. Unit Operations
3. Process Control
4. Safety and Environmental Considerations
5. Chemical Reactions
6. Energy Efficiency
7. Process Modeling and Simulation
8. Quality Control
9. Regulatory Compliance
10. Process Optimization
11. Emerging Technologies
When it comes to prevention of industrial accidents, these become very prominent aspects especially during development of new Chemicals, Active Pharmaceutical Ingredients (APIs), and Drug Products as well as during their Technology Transfer (commercialization from lab/pilot to commercial scale).
Integrating EHS and ESG considerations into the development of new Chemicals, Active Pharmaceutical Ingredients (APIs), and Drug Products is crucial to ensure that these products are safe to manufacture, environmentally responsible, and compliant with regulations, which can bring a significant competitive advantage in today’s markets.. We help clients deploy the key principles and practices for managing EHS during the development of chemicals, APIs, and drug products that include Regulatory Compliance, Risk Assessment, Green Chemistry Principles, Material Selection, Process Safety, Pollution Prevention, Waste minimization & responsible disposal, Occupational Safety, Training, Waste Management, Emergency Preparedness, Transportation Safety, Environmental Impact Assessment, Life Cycle Assessments, Collaborate with EHS Experts, Continual Improvement, EHS Documentation, Supplier Engagement etc.
EHS during Technology Transfer process for chemicals, Active Pharmaceutical Ingredients (APIs), and Drug Products – Technology transfer involves transferring knowledge, processes, and manufacturing capabilities from one location or organization to another, often during the development, scale-up, or commercialization phases. We support clients in a structured management of EHS aspects which ensures that the transfer is conducted safely, compliantly and in an environmentally responsible manner. We consider the aspects like EHS Due Diligence through Risk Assessment, Regulatory Compliance, Documentation and Knowledge Transfer, Safety Protocols, Hazardous Materials Handling, Process Safety Management, Occupational Safety, Industrial Hygiene, Waste Management, Environmental Impact, Emergency Response, training etc.
Properly managing EHS during technology transfer not only ensures regulatory compliance but also minimizes risks, protects employees and the environment, and maintains the integrity of the transferred technology. Effective collaboration between sending and receiving sites, thorough assessments, and a commitment to EHS best practices are essential for a successful and safe technology transfer in the chemical, API, and drug product industries.
The purpose of DfSE in the Process Industry is to integrate safety and environmental considerations into the early stages of the design and development of chemical processes, products, and facilities. DfSE aims to proactively identify, mitigate, and prevent safety hazards and environmental risks, ultimately enhancing the overall sustainability and safety of chemical processes. DfSE is a proactive and forward-thinking approach that not only enhances safety and sustainability but also leads to cost savings and improved efficiency. Two key elements play a vital role in having Right First Time, the EHS and ESG aspects. These are site selection and siting layout.
Selecting a greenfield site for establishing an industrial facility requires careful consideration of various EHS and ESG aspects to ensure regulatory compliance, minimize environmental impacts, and create a safe and sustainable operation. Site selection for a chemical industry facility is a critical decision that can significantly impact long-term EHS performance and regulatory compliance. We help in conducting thorough assessments and addressing all EHS and ESG aspects during the site selection process that will help ensure the responsible and sustainable development & expansion of the facility.
Siting Layout of Chemical, Active Pharmaceutical Ingredient (API), and Pharmaceutical facilities are critical considerations that impact safety, Operability, efficiency, regulatory compliance, and overall operations. Designing an effective site layout requires careful planning and adherence to industry best practices and safety standards. Our experts help in setting out the requirements by considering multiple key aspects such as Regulatory Compliance, Safety and Process Flow, Zoning and Land Use, Environmental Considerations, Process safety including Safety Zones, Equipment Placement, Security and Access Control, Utilities and Infrastructure, Emergency Response and Fire Safety, Material Handling and Storage, Support Services, Employee Facilities, Building Design, Waste management, Green Practices and Sustainability, Site Accessibility, Future Expansion planning, EHS Management Systems, Worker Safety, Community Engagement etc. to name a few.
A multidisciplinary team of professionals, including EHS experts, Engineers, and Specialists collaborate on the site layout and design to ensure that it meets all safety, regulatory, and operational requirements. Additionally, we help conduct regular reviews and assessments of the site layout to adapt to evolving industry standards and changing business needs.
Risk assessment is a systematic process that involves identifying, evaluating, and mitigating potential risks or hazards in various contexts, such as workplace safety, environmental management, financial planning, and more. The goal of risk assessment is to make informed decisions that minimize or control risks and maximize opportunities. Some of the important techniques are:
JSA (Job Safety Analysis) – JSA is a systematic process used to identify potential hazards associated with specific job tasks. It aims to assess risks and develop controls to ensure the safety of employees while performing their duties.
PHA (Process Hazard Analysis) – PHA is a comprehensive assessment of the potential hazards and risks associated with a chemical process or facility. It involves the systematic examination of processes, equipment, and operations to identify and mitigate potential hazards.
HAZID (Hazard Identification Study) – HAZID is a structured process used to identify and assess hazards associated with a project, facility, or system at an early design stage. It helps in the early identification and elimination or mitigation of potential risks.
HIRA (Hazard Identification and Risk Assessment) – HIRA is a systematic approach to identifying, evaluating, and prioritizing risks and hazards in a given environment or process. It includes the assessment of consequences and likelihood to determine risk levels.
EAA (Environmental Aspect and Impact Assessment) – EAA is a process used to identify and evaluate the environmental aspects and potential impacts of an organization’s activities, products, or services. It helps organizations manage their environmental responsibilities.
HAZOP (Hazard and Operability Study) – HAZOP is a structured and systematic examination of a process to identify deviations from design intent that can lead to hazards or operability issues. It is commonly used in the chemical and process industries.
What-If Analysis – What-If Analysis is a qualitative risk assessment technique where a team explores various hypothetical scenarios to identify potential hazards and assess their impact on a process or system.
Antimicrobial Resistance Risk Assessment (AMR Risk Assessment, AMRRA) – An effective AMR Risk Assessment is a crucial tool in the global effort to combat antimicrobial resistance, as it helps policymakers, healthcare professionals, and researchers make informed decisions to reduce the spread of resistant microorganisms and preserve the effectiveness of existing antimicrobial treatments. AMRRA is a systematic evaluation process used to identify, quantify, and understand the potential risks associated with the development and spread of AMR in various settings of manufacturing operations, distribution and the environment.
Laboratory RA (Laboratory Risk Assessment) – Laboratory RA is the process of identifying and evaluating risks associated with laboratory experiments, procedures, and activities. It aims to ensure the safety of laboratory personnel and minimize potential hazards.
SIMOPs RA (Simultaneous Operations Risk Assessment) – SIMOPs RA is a method used to assess and manage risks when multiple simultaneous operations are taking place within a facility. It helps ensure that these activities can be conducted safely and without interference.
COSHH Assessment – Part of Occupational health and Industrial hygiene that focuses on identifying and controlling workplace hazards to protect workers’ health. COSHH (Control of Substances Hazardous to Health) assessment is specific to the management of hazardous substances in the workplace.
Qualitative Workplace Exposure Assessment (WEA) is a qualitative evaluation of workers’ potential exposure to hazards in the workplace. It helps identify areas where further exposure assessment or control measures may be needed.
Human Error Assessment (HEA) – Human Error Assessment involves the systematic evaluation of human actions and decisions within a specific operational context to identify the potential for errors and their consequences. The goal is to prevent or mitigate errors that could lead to safety incidents.
Safety Critical Task Analysis (SCTA) – Safety Critical Task Analysis focuses on tasks and activities that have a high impact on safety if errors occur. It is often used in safety-critical industries such as aviation, where human error can have severe consequences.
Process Safety Management (PSM) is a critical framework for managing the risks associated with hazardous processes in industries such as chemicals, oil and gas, and manufacturing. A PSM gap assessment is a systematic evaluation of an organization’s current PSM practices and the identification of areas where there are gaps or deficiencies in compliance with PSM regulations or industry best practices. Once gaps are identified, mitigation plans are developed to address these shortcomings and improve overall process safety.
Managing Risks
Safe Operating and Maintenance Procedures are essential in industry to ensure the safety of personnel, protect equipment, promote a culture of safety, and ensuring that tasks are performed correctly thus help prevent accidents / incidents. These procedures provide step-by-step instructions on how to perform tasks and operate machinery or equipment safely. We support clients for developing and implementing safe operating and maintenance procedures by bringing in best practices. Some of the key elements include Task Analysis, Identify Safety Precautions, Develop Detailed Procedures, Use Standardized Formats, Training and Competency, Safety Documentation, Hazard Communication:, Emergency Procedures, Lockout/Tagout/Tryout (LOTOTO), Regular Review and Revision, Supervision and Oversight, Reporting and Incident Investigation, Accessibility and Availability.
EHS Dossier and Documentation is a critical element to O&M and refers to a comprehensive collection of documents, records, and information that an organization maintains to demonstrate its compliance with EHS regulations and standards, track its environmental and safety performance, and manage EHS-related risks. It is a critical component of responsible environmental stewardship and workplace safety. Effective EHS dossier and documentation management is crucial for legal compliance, risk reduction, and promoting a culture of safety and sustainability. An organized and well-maintained EHS documentation system is fundamental to achieving a safe and environmentally responsible workplace. Proper EHS documentation is crucial for quick and easy retrieval, regulatory compliance, risk management, incident reporting, and demonstrating a commitment to EHS standards. This also includes setting up documentation systems for Accessibility and Security.
Permit to Work (PTW) System is a safety management tool used to control and manage high-risk activities. It clearly defines & control the shift of responsibilities. Its benefits include enhanced safety, risk reduction, clear communication, accountability, compliance, and the promotion of a safety-oriented culture. Implementing a PTW system ultimately protects both employees and the organization from potential harm and liabilities.
EHS MOC is a systematic & structured process used to evaluate and control the potential risks associated with changes in an organization’s operations, processes, equipment, or facilities. Proper MOC procedures are essential to ensuring accident prevention, maintain safety of employees, protect the environment, and compliance with regulations. We support clients in setting up effective EHS Management of Change through setting processes and systems that enable Identify Change Initiatives, Pre-Change Review to evaluate and assess risks, Documentation, Review and Approval, Impact Analysis, Risk Mitigation, Communication, Implementation, Post-Change Review through Monitoring and Auditing, Record Keeping, Training and Competency and Management Oversight.
Effective EHS Management of Change ensures that organizations can adapt to evolving circumstances while safeguarding the well-being of employees, minimizing environmental impact, and remaining in compliance with regulations. It is a proactive approach to managing risks associated with workplace changes and innovations.
PSSR is a critical phase in the management of process safety for industrial facilities, particularly those in the chemical, petrochemical, and manufacturing industries. The primary purpose of a PSSR is to ensure that a new or modified process, facility, or piece of equipment is safe to operate before it is commissioned and starts production. PSSR is a proactive measure that helps prevent accidents, injuries, and environmental incidents during the start-up phase of a new process or facility. It ensures that safety is a top priority and that all necessary precautions have been taken before operations commence.
By following a structured incident investigation and recurrence prevention process, organizations can not only understand the causes of incidents but also share such undesired events (internal and external) internally across operations that help take proactive measures to prevent similar occurrences, ultimately creating a safer work environment and reducing risks.
We help set systems that comprehensively covers Immediate Response, Notification and Reporting, Preserve the Scene, Investigation Team Formation, how to Gather Information, conduct efficient and quality Root Cause Analysis, Incident Report, CAPA that include process changes, training, equipment upgrades, or policy revisions & Implementation, Review and Follow-Up, Documentation and Records, Communication, and Continuous Improvement where organizations can use the lessons learned from incidents to enhance safety protocols, training programs, and risk management strategies.
Asset integrity and reliability are essential for organizations to maintain safe and efficient operations, reduce downtime, and optimize asset performance. These concepts involve a combination of preventive measures, proactive maintenance strategies, risk assessment, compliance with industry standards, and continuous improvement efforts to ensure assets fulfill their intended functions effectively and consistently.
This broadly involves management of EHS Controlled and Critical Equipment as vital to ensure the safety of personnel, protect the environment, and maintain the integrity of equipment deployed on critical processes or systems.
We guide organizations to managing these equipment effectively through focus on their classification & identification; Inventory and Documentation; Risk Assessment; Regulatory Compliance; Preventive Maintenance; Emergency Response Plans; Training and Competency; Equipment Testing and Certification advisory; Spare Parts Inventory esp. insurance spares; Safety Measures; Equipment Retirement and Replacement; Incident Reporting and Investigation.
Effective management of controlled and critical equipment is integral to EHS management systems, ensuring that organizations operate safely, efficiently, and in compliance with regulations. Regular maintenance, risk assessments, and a proactive approach to safety help minimize risks associated with these equipment types.
EHS training is a fundamental component of a successful EHS program and plays a critical role in enhancing the performance of individuals and organizations in terms of safety, compliance, and overall sustainability. It is an investment in the well-being of employees, the protection of the environment, and the overall performance and reputation of an organization. Effective EHS training programs contribute to a safer workplace, regulatory compliance, reduced incidents, improved employee morale, and a stronger commitment to environmental responsibility. Effective training programs not only enhance safety but also contribute to long-term sustainability and success.
EPR are essential components of an organization’s overall safety and risk management strategy and are vital aspects of safeguarding an organization’s people, assets, and reputation. These processes involve the preparation for and management of various emergencies, including natural disasters, industrial accidents, fires, medical crises, and other unexpected events that could disrupt normal operations and pose risks to people, property, and the environment. Effective planning, training, and coordination ensure that an organization can respond to emergencies efficiently and minimize the impact of adverse events.
Contractor and vendor EHS management is a crucial aspect of ensuring that all parties involved in a project or business operation prioritize safety and adhere to EHS standards and regulations. Integrating EHS with ESG ensures that all parties not only prioritize safety but also adhere to broader sustainability and ethical principles. When contractors and vendors work on your site or project, their actions can significantly impact the overall safety and environmental performance. Their management involve the integrated EHS and ESG considerations into the selection, oversight, and collaboration with them. Effective contractor and vendor EHS management not only protect the safety and well-being of everyone involved but also minimize operational disruptions, reduce liabilities, and enhance the overall sustainability of projects and operations. It requires ongoing collaboration, communication, and a shared commitment to EHS excellence.
Another important aspect relates to EHS in Contract Manufacturing which involves the management of EHS risks and compliance by both the contracting company (the client) and the contract manufacturer (the supplier). This collaboration is crucial to ensure that products are manufactured safely, meet quality standards, and comply with relevant regulations thereby ensuring supply and hence business continuity. We support clients in Supplier Due Diligence and Selection, Clear Contracts and Agreements by defining EHS expectations, responsibilities, and requirements in the contract or agreement between the client and the contract manufacturer, Risk Assessment, setting Safety Protocols, Training and Competency building, Incident Reporting and Investigation, Auditing and Inspection, Emergency Response Plans, Material Handling:, Waste Management, Documentation and Reporting, and EHS Communication.
Effective EHS management in contract manufacturing requires collaboration, communication, and a shared commitment to safety and environmental responsibility. Both parties must work together to ensure that products are manufactured with the highest regard for EHS standards and practices.
Auditing and Performance Reviews
EHS KPIs and Governance involves the establishment of policies, procedures, and systems to manage and monitor an organization’s EHS performance. Key Performance Indicators (KPIs) play a critical role in measuring and tracking the effectiveness of EHS governance efforts. EHS KPIs provide organizations with a comprehensive toolset for measuring and improving their environmental sustainability, health, and safety performance. By effectively tracking these metrics, organizations can realize numerous benefits, including cost reduction, risk mitigation, improved safety culture, and enhanced reputation, all while contributing to a safer, more sustainable future. Effective EHS governance with well-defined KPIs and robust tracking mechanisms not only helps ensure regulatory compliance but also enhances sustainability, reduces risks, and improves the overall health and safety of employees and the environment.
We help to developing and tracking EHS KPIs through defining EHS Objectives & assign Relevant KPIs for aspects covering Environmental, Health and Safety, and Compliance. This enables organizations to Set Baselines and Targets, Implement Data Collection Monitoring and Reporting, defining CAPA, Communicate Results to internal and external stakeholders, Benchmark against peers, Audits and Review to ensure that it remains effective and aligned with organizational goals.
Our major focus is on Leading indicators that are proactive metrics and valuable tools that provide insights into an organization’s performance in preventing incidents, identifying potential risks, and promoting a culture of safety. Their benefits include early risk detection, improved safety culture, legal compliance, resource allocation, and the promotion of a positive reputation. Leading indicators empower organizations to prevent incidents, protect employees, and reduce environmental impact while fostering a culture of safety and sustainability.
Process Safety Management audits, are a systematic and comprehensive examination of an organization’s process safety management system. These audits are conducted to assess the effectiveness of process safety controls, practices, and procedures in place to prevent accidents, incidents, and catastrophic events in industries where hazardous chemicals and processes are involved, such as chemical manufacturing and pharmaceuticals. PSM audits are critical for preventing catastrophic incidents, protecting workers, and minimizing the environmental impact of process-related activities. They help organizations identify weaknesses in their process safety systems and ensure that necessary corrective actions are taken to reduce the risk of accidents and incidents.
Management EHS reviews and continual improvement are integral components of an organization’s commitment to safeguarding the environment, protecting the health and safety of employees, and enhancing its overall sustainability performance. These processes involve regular assessments of EHS programs, policies, and performance, followed by action plans to address deficiencies and drive ongoing improvement.
Key Benefits include Improved EHS performance and compliance with regulations, Reduced incidents, injuries, and environmental impact, Enhanced safety culture and employee engagement, Greater sustainability and responsible business practices, Stronger reputation and stakeholder confidence, Long-term sustainability and resilience in the face of changing EHS challenges.
Management EHS reviews and continual improvement are essential processes for organizations committed to achieving excellence in EHS and sustainability. These processes enable organizations to adapt to evolving EHS standards, reduce risks, and contribute to a safer, healthier, and more sustainable future.